全工程のデジタル化で生産性向上
「DXの内製化」目指す
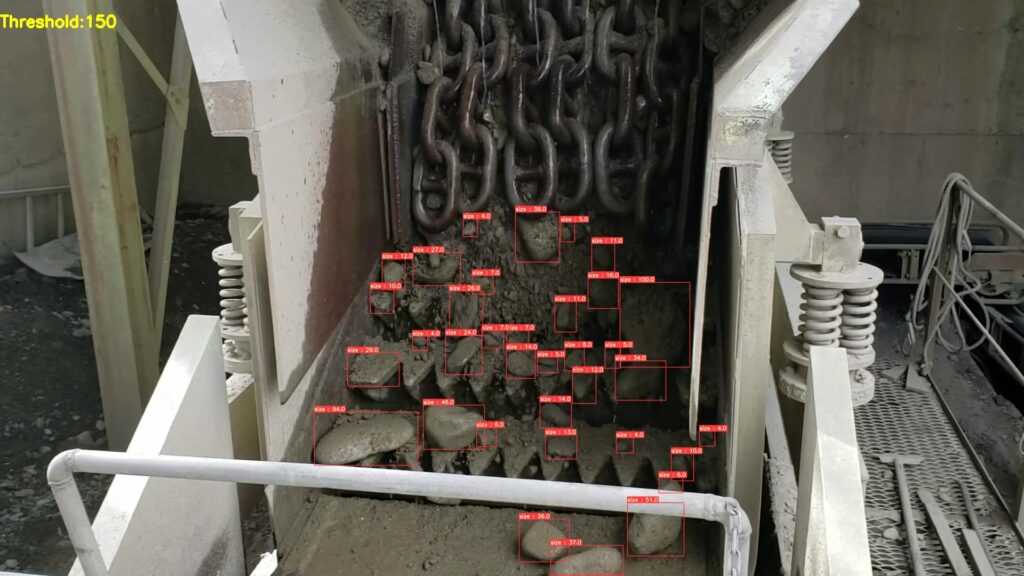
ヤマサ(松本市、北爪寛孝社長)は、骨材に使う砕石や砂利などの原石のサイズをAIで判別するシステムを開発し、2022年1月に特許を取得した。自社工場での試験導入による実証を重ね、骨材製造の全工程をデジタル化することで生産性の向上を図る。

同社が開発した「原石判別AIシステム並びに骨材製造最適化システム(G-MOS)」は、採取箇所ごとの原石の状態をAIで判別し、最適な採取箇所を把握することができるもの。工区ごとに原石の状態を記録することで採取に適した工区の予測に活用することが可能だ。
これまでの採取作業では、「現場作業員の経験に頼らざるを得ず、質より量が求められてきた」(北爪社長)ところを、「経験が浅い若年者でも負担なく製造効率を向上できる」。このほか「作業にかかるCO2排出量やエネルギーコストの削減にも貢献し、事業継続性の向上につながり、さらに、製造工程が数値化されることで物流における原石の積載状態を最適化することもできる」。また、「安定した破砕機の稼働につながり、設備のダメージを軽減できる」などメリットは多いという。

「長年オーソドックスなスタイルで運営されてきた骨材製造事業を、サステナブルとデジタルの2つの視点で効率的に見直すことができ、新たな可能性を見出すことができた」とする。
開発にあたり、北爪社長はDXの内製化にこだわったという。外注では費用と時間がかかるものの「十分な成果を出せずにいた」。そこで「求人倍率が最も高いとされるITエンジニアの採用に踏み切った」。地元出身のITエンジニアに、「製造工程を隅々まで見てもらい、課題を共有した」と話す。
「事例としてまずは同業界から広げていきたい」と話している。
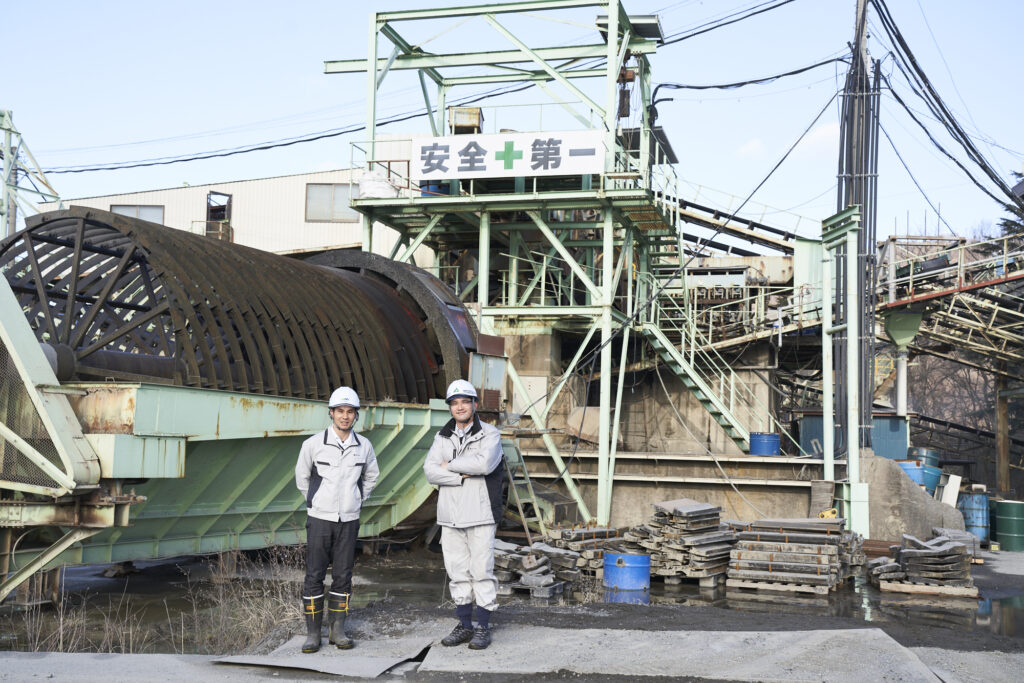
【お問い合わせ】株式会社ヤマサ
〒399‐8715 長野県松本市大字笹賀7600-22 担当:筒木 mail:pr.d@s-yamasa.co.jp